How to Professionally Perform a Tile Take-Off: A Comprehensive Guide for Builders and Tiling Companies
Everything You Need to Know About Estimating Tiles for residential, commercial and industrial projects.
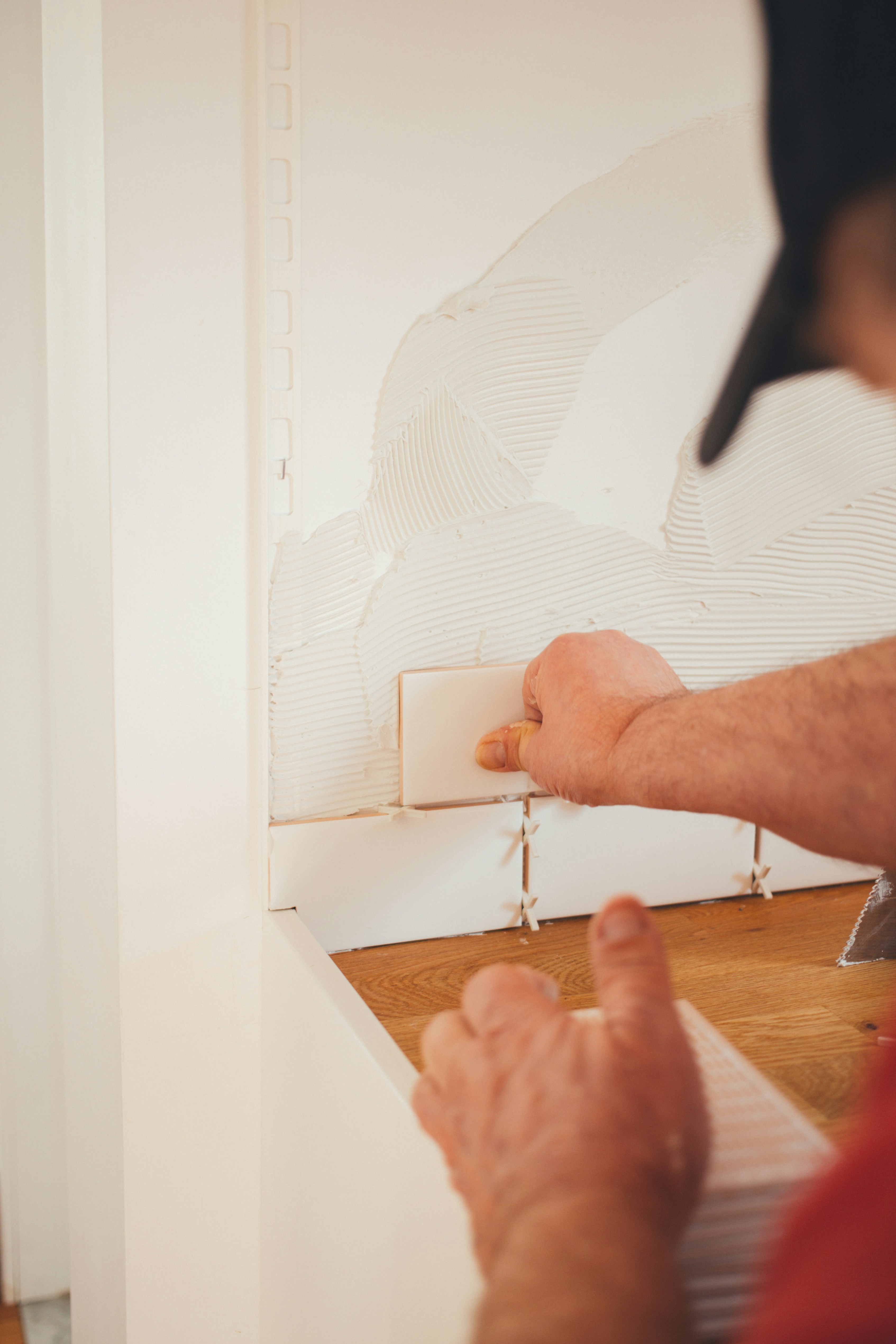
How to Professionally Perform a Tile Take-Off: A Comprehensive Guide for Builders and Tiling Companies
Tiling is one of the most widely used finishes in Australian construction due to its unparalleled durability, versatility and aesthetic appeal. Tiles provide a robust, hard-wearing surface that can endure heavy foot traffic, making them ideal for both residential and commercial applications. Their resistance to moisture, stains and heat makes them particularly suitable for Australia's varied climate and common use in wet areas such as bathrooms, laundries and kitchens. Beyond functionality, tiles also offer an extensive range of design options, from timeless classics to contemporary finishes, enabling seamless integration with any architectural or interior style. Additionally, their ease of maintenance and long lifespan make them a cost-effective and practical choice for builders and homeowners alike.
Estimating Tiling from a Comprehensive Perspective
To professionally estimate tiling, it’s essential to breakdown every component that contributes to a complete and high-quality finish. This includes not only floor and wall tiling but also the essential sub-trades and preparatory works required to meet Australian standards and project-specific requirements. Key elements include:
- Floor and wall tiling
- Waterproofing
- Screeding
- Trims
- Angles
- Caulking
- Control joints
- Expansion joints
- Sealing
- Acoustic underlay (if applicable)
- Pedestal system (typically balconies)
Each component is vital to the overall durability, functionality and aesthetic of the tiling package. Accurate material usage and compliance with standards ensure project success while minimising costs and waste.
Developing an Accurate Estimate
In this section, we will use a standard bathroom layout to break down and calculate each of the listed components individually. The example bathroom represents a typical size commonly found in Australian homes, featuring tiled floors and walls. This layout provides an excellent basis to demonstrate how to accurately account for all materials and labour required for a complete tiling package.
Floor Tiling
When measuring bathroom floor tiles from a plan, the first step is determining the total floor area. Multiply the length and width of the bathroom, keeping any irregular sections in mind and deducting fixed features like bathtubs, vanities, or built-in cabinetry that won’t require tiling. Ensure the tile dimensions align with the plan and always double-check your calculations against the drawing scale to minimise errors.
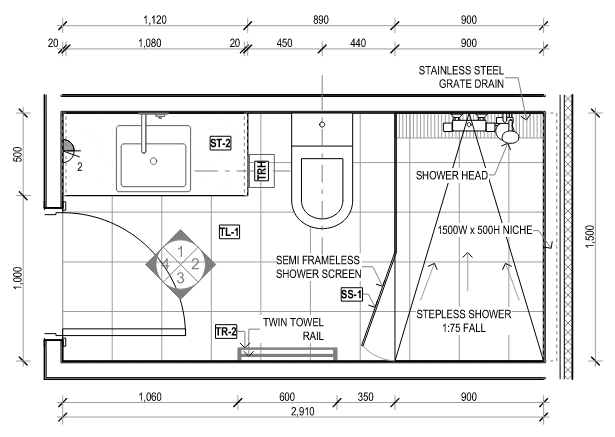

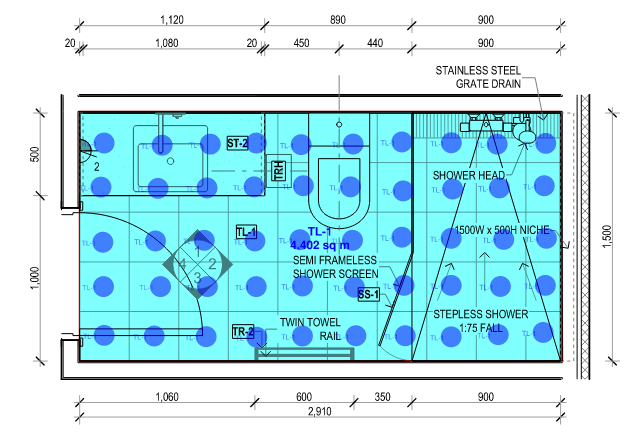
For example, in a bathroom with dimensions 2.91m (length) and 1.50m (width), the total area is:
2.91 x 1.50 = 4.365m², which rounds to 4.40m².
Using a digital take-off tool like Bluebeam can further validate your manual calculations. In this instance, the tool measured the area at 4.402m², a negligible difference.
At this stage, many estimators would apply a standard 10% wastage allowance, resulting in 4.84m². However, this approach often underestimates the true number of tiles required. To avoid running short on-site, a tile count is essential.
In this example, the floor tile (TL-1) is 300 x 300mm. Counting tiles reveals 50 tiles are needed, calculated as:
50 x 0.3 x 0.3 = 4.50m² (the raw tile quantity, excluding wastage).
Next, determine how many tiles fit in a box. Typically:
- A 300 x 300mm tile covers 0.09m².
- Manufacturers pack tiles to cover 1m² or more per box.
- For this example: 1 ÷ 0.09 = ~ 11.11 tiles per box (rounded to 12), covering 1.08m² per box.
Converting 50 tiles into boxes gives:
50 ÷ 12 = ~ 4.16 boxes, rounded up to 5 boxes (5.4m² or 60 tiles).
But are 60 tiles enough? Probably not. An additional allowance for breakages, off-cuts, and human error is vital. Adding another box (12 tiles) provides extra coverage and leaves spare tiles for future maintenance.
Final recommendation:
Total tiles required: 72 tiles (6.48m² or 6 boxes).
This highlights the disparity between initial estimates (4.84m²) and the final supply requirement (6.48m²). The true wastage factor in this case is:
6.48 ÷ 4.84 = ~ 33.8%, far exceeding the typical 10% allowance.
Wall Tiling
Accurately estimating wall tiles involves more detailed calculations due to multiple elevations and varying dimensions. Start by measuring each wall (Elevation 1-4) using plan elevations and a digital take-off tool to determine the total area. Avoid deducting areas such as mirrors, toilets, or floating vanities unless specified in the scope.
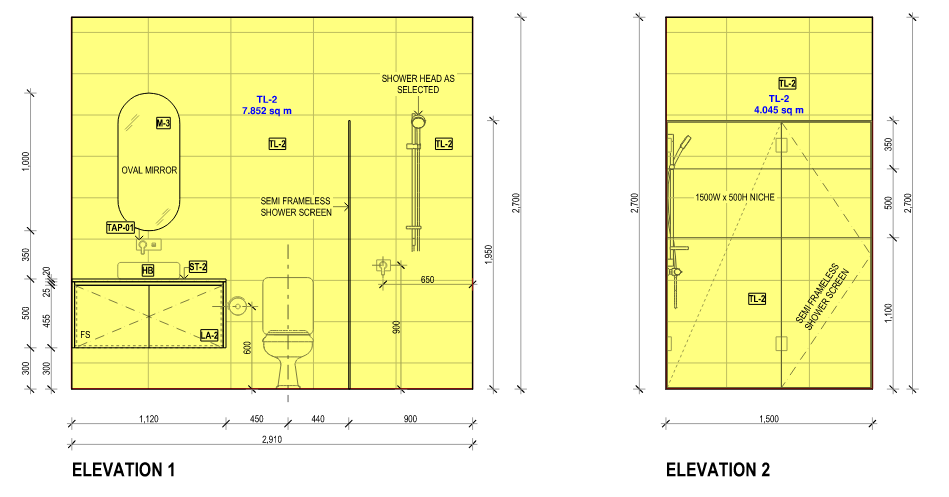
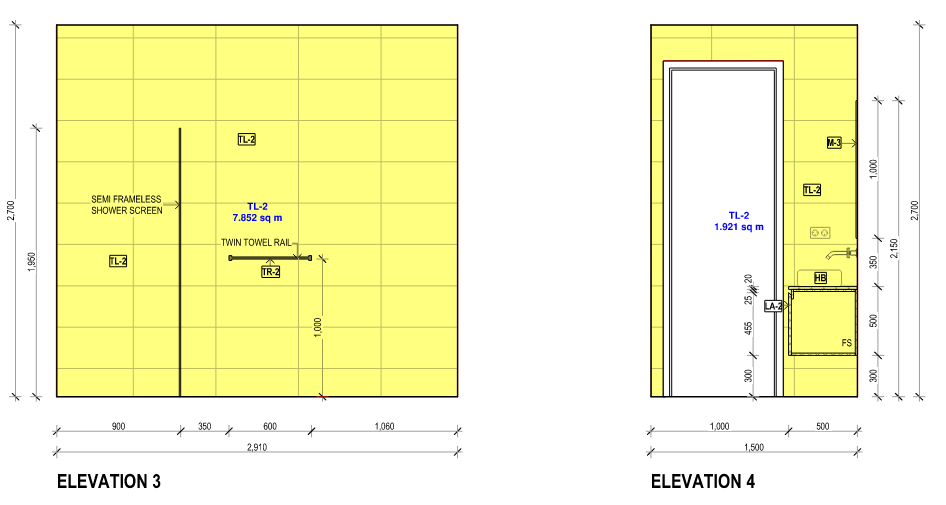
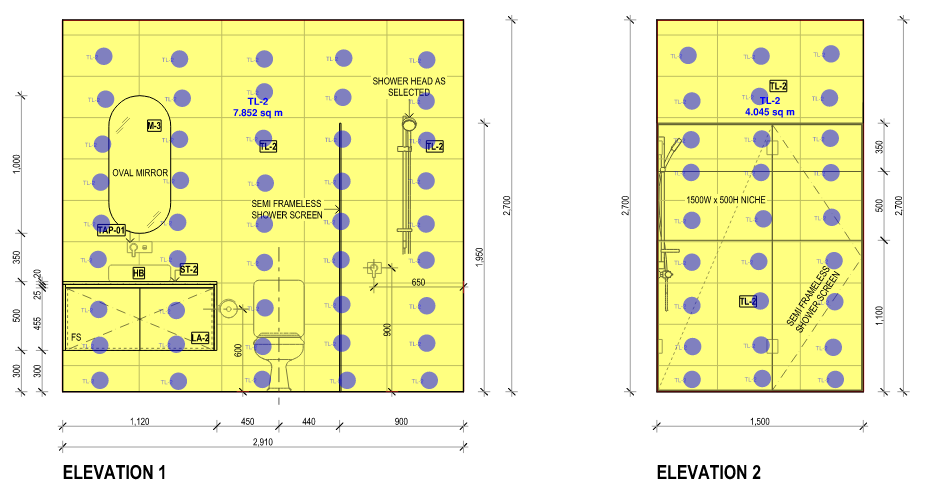
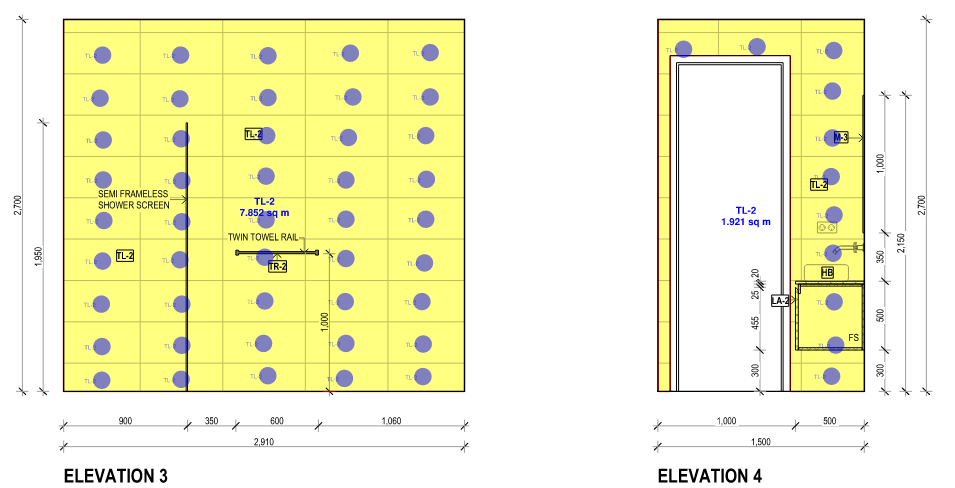
The nominated wall tiles, identified as TL-2, measure 300 x 600mm, resulting in the following calculations:
Elevation 1: 7.852m², or 45 full tiles and 3 cut tiles = 48 tiles x (0.3 x 0.6) = 8.64m²
Elevation 2: 4.045m², or 27 full tiles and 2 cut tiles = 29 tiles x (0.3 x 0.6) = 5.22m² (including niche)
Elevation 3: 7.852m², or 45 full tiles and 3 cut tiles = 48 tiles x (0.3 x 0.6) = 8.64m²
Elevation 4: 1.921m², or 11 full tiles and 6 cut tiles = 17 tiles x (0.3 x 0.6) = 3.06m²
The total quantity of tiles required comes to 25.26m² or 142 tiles as a bare minimum, excluding packaging, breakages and wastage.
You might wonder why all tiles, such as those in the top row, niche and around door frames, haven’t been individually highlighted. The reason is straight forward cut tiles have been treated separately, reflecting a realistic "hit and miss" approach based on how a tiler would install them. Every tiler has their own methodology, and unless closely monitored, they may not track off-cuts or make efficient use of them. It’s common for tilers to default to a new tile rather than reusing cuts unless specifically instructed for certain areas.
How much wastage should you allow for the walls? Is one box sufficient?
The answer is likely no, and this is where experience and consultation with your installer are invaluable.
Given the tile size of 300 x 600mm, one box typically contains 8 tiles or 1.44m².
- 142 tiles ÷ 8 tiles per box = 17.75 boxes
- Rounded up to 18 boxes: 18 x 1.44 = 25.92m²
- Allowing for one additional box to cover wastage and future maintenance, the total comes to 27.36m² or 152 tiles.
If you only followed area calculations (7.852 m² + 4.045 m² + 7.852m² + 1.921 m²)
Total area = 21.67m² with 10% wastage = 23.837m²
This shows the default wastage factor would not be sufficient for accurate ordering. In this example, the true wastage factor for the walls is 27.36 ÷ 21.67 = 26.2%.
One of the most significant issues with under-ordering tiles, particularly on larger projects, is the challenge of sourcing tiles with the same batch number. Typically, there may be multiple batch numbers for the same tile, and while they are intended to match, slight variations in colour, tone, and finish can occur. These differences, although subtle, can become highly noticeable when tiles from different batches are laid in the same area, disrupting the uniformity of the finish.
This issue becomes even more pronounced on large-scale projects such as apartment developments, where consistency across large spaces is essential to maintain quality and aesthetic appeal. Imagine a situation where additional tiles are needed partway through the project, and the supplier can only provide tiles from a different batch. The variation in appearance could lead to costly rework, disputes with clients, or even compromise the project's reputation.
To avoid such problems, it’s absolutely critical to calculate and order the correct quantity of tiles right from the start. Factoring in wastage, breakages and the need for spares is essential, as is consulting with your supplier to ensure sufficient stock from the same batch. Not only does this help maintain visual consistency, but it also prevents delays and unnecessary expenses caused by sourcing mismatched replacements during construction. Planning ahead and ordering accurately is always more cost-effective than risking the repercussions of short ordering.
Waterproofing
Waterproofing is a critical component of construction in Australia, ensuring moisture protection for wet areas such as bathrooms, laundries, and kitchens. Adhering to AS 3740:2021 – Waterproofing of Domestic Wet Areas is essential to achieve compliance and longevity.
Key requirements include:
- Showers: Entire shower floors must be waterproofed, and walls must be waterproofed to a minimum height of 1800mm.
- Vanities: The junction between the wall and vanity must be sealed to prevent water ingress.
- Bathrooms: Bathroom floors require waterproofing up to 150mm above the floor level or higher where required by design.
- Perimeter walls: Horizontal junctions must have waterproofing extending at least 100mm up walls, ensuring all wet zones are adequately protected.
Proper waterproofing not only complies with Australian Standards but also prevents structural damage, mould growth and costly repairs. Engaging qualified professionals and using compliant materials is crucial for delivering robust and long-lasting results.
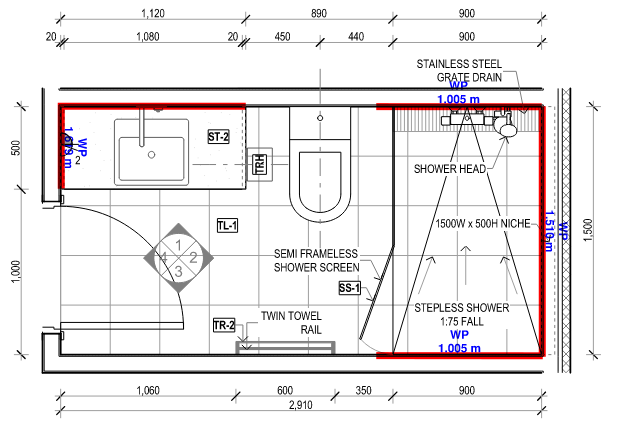
Waterproofing calculations consist of the following:
Floor: 2.91 x 1.5 = 4.365m²
Floor above screed: 0.9 x 1.5 = 1.35m² (Only applicable to the shower base)
Floor returns (150mm high): (2.91 + 2.91 + 1.5 + 1.5) – 0.82 (door opening) = 8.00m x 0.15 = 1.20m²
Shower enclosure up to 1800mm high: (1 + 1 + 1.5) x 2.0 = 7.00m² (A rule of thumb is to allow 100mm above the showerhead and beyond shower screen. In this case, the showerhead is located at around 1900mm high, so waterproofing is allowed up to 2000mm high.)
Vanity up to 200mm high: 1.08 + 0.5 = 1.58 x 0.2 = 0.316m²
Therefore, the total waterproofing required is:
Floor: 4.635m² + 1.35m² + 1.20m² = 7.185m²
Walls: 7.00m² + 0.316m² = 7.316m²
Screeding
Screeding is a crucial step in preparing a level substrate for flooring in Australian construction projects, ensuring proper load distribution and adherence to finish specifications. In line with AS3958.1-2007: Ceramic tiles – Guide to the installation of ceramic tiles, screeds must be installed with a minimum thickness of 40mm for bonded screeds and 50mm for unbonded screeds to ensure durability and prevent cracking. For falls to drainage, particularly in wet areas, AS 3740-2021: Waterproofing of domestic wet areas recommends a minimum fall of 1:100 to comply with proper water management.
High-quality screeding is essential for meeting Australian standards, providing a sound, level surface while ensuring compliance with waterproofing, tiling and structural integrity requirements.
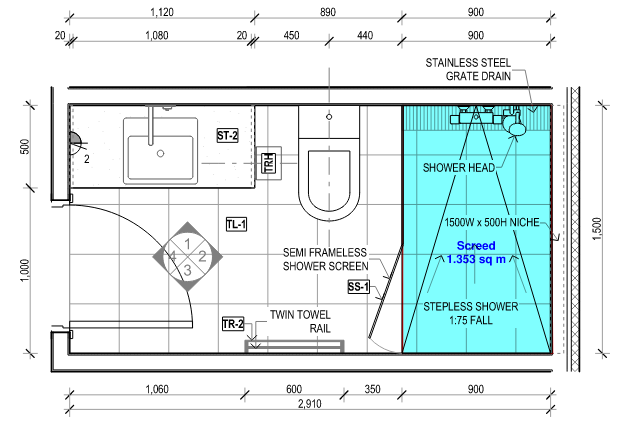
Screed calculations are as follows:
Shower base only = 0.9m x 1.5m = 1.35m², up to 40mm thick.
Trims
Floor and wall trims play a vital role in achieving a polished, professional finish in tiling projects across the Australian construction sector. These trims, typically made from materials like aluminium, stainless steel, or PVC, are used to protect tile edges, cover gaps, and create seamless transitions between different surfaces. Floor trims are essential for areas such as doorways or where tiles meet other flooring types, while wall trims are commonly used to cap exposed edges, such as around niches, window reveals, or external corners. In addition to their functional purpose, trims enhance the aesthetic appeal of tiled surfaces, providing clean lines and a cohesive look. With a wide range of profiles, finishes, and sizes available, trims can be tailored to suit any design while meeting the durability requirements of Australian building standards.
Trim calculations are as follows:
Door trim: 0.820m
Niche trim: 1.5m x 2 = 3.00m (only for the horizontal sides; vertical trims are not required as tiles run to the edge).
Total trim required = 3.82m
Angles
Shower angles play a critical role in achieving proper water drainage and maintaining compliance with waterproofing standards in Australian bathrooms. Under the National Construction Code (NCC) and AS 3740:2021 – Waterproofing of Domestic Wet Areas, shower areas must incorporate adequate falls to floor wastes, ensuring water does not pool or escape beyond designated wet zones.
A perimeter angle (often aluminium or stainless steel) is typically required to create a defined edge where falls transition to adjoining dry areas, especially in open-plan or curb less showers. However, the need to extend a perimeter angle across the entire bathroom depends on whether the space is classified as a "fully enclosed wet area" or an open-plan design.
According to AS 3740, a perimeter angle is required throughout the bathroom if:
- The entire bathroom is waterproofed, rather than just within the shower zone.
- Falls to floor wastes are consistent across the entire area, as in fully tiled, wet room designs.
- The design lacks physical barriers (e.g., hobs or shower screens) to separate wet and dry areas.
In such cases, the angle provides a structural and aesthetic solution, aiding in fall transitions and ensuring compliance with waterproofing and drainage standards. By following these guidelines, builders can prevent water ingress and ensure a durable, NCC-compliant finish.
Shower angle calculations are as follows:
Shower perimeter: 1.5m x 2 + 0.9m x 2 = 4.8m. (Realistically, due to the fall, the shower angle is probably not required on all sides and is only applicable to the visible side, which is the shower door side only 1.5m long.)
Caulking
Caulking plays a vital role in the Australian construction industry, particularly in ensuring waterproofing and sealing in wet areas such as bathrooms. It involves applying a flexible sealant to gaps, joints, and transitions between materials to prevent water ingress, enhance aesthetics, and accommodate minor movements in the building structure.
- Material Selection: Use mould-resistant, flexible silicone or polyurethane sealants rated for wet areas. Ensure compatibility with surrounding materials such as tiles, stone, or acrylic fixtures.
- Joint Preparation: Clean and dry all surfaces before applying the sealant. Use a primer where necessary, especially with porous substrates, to ensure adhesion.
- Application: Seal joints at all wall-to-floor and wall-to-wall transitions, around fixtures (e.g., sinks, bathtubs, and shower screens), and between tiled surfaces. Maintain a minimum joint width of 6mm, allowing for adequate flexibility and movement.
- Finishing: Smooth the sealant with a finishing tool to ensure a consistent, watertight bead. Remove excess sealant immediately to avoid surface staining.
- Cure Time: Allow sufficient curing time as recommended by the sealant manufacturer before exposing the area to water.
By adhering to these standards and best practices, caulking can significantly extend the lifespan of wet areas and prevent costly water damage in Australian construction projects.
Caulking calculations are as follows:
Floor: (2.91 x 2 + 1.5 + 1.5 - 0.82) = 8.00m
Wall: Corners (4 No.) x 2.7m (ceiling height) = 10.8m
Ceiling: Same as floor but include door = 8.82m
Toilet: Allow 1.0m to base
Mirror: 2.50m
Vanity: Allow all visible sides (1.12 + 0.5) top and vertical sides (0.5 + 0.5) = 2.62m
Door frame: (2.34 x 2) + 0.872 = 5.552m
Niche: (1.5 + 1.5 + 0.5 + 0.5) + 0.08 x 4 = 4.32m
Therefore, the total caulking required is approximately 43.61m ~ 44.00m (caulking only allowed to tiled areas)
Control Joints
Control joints are crucial in construction to manage movement in materials caused by thermal expansion, contraction, or structural settlement. They prevent unsightly cracks and maintain the structural integrity of surfaces, particularly in tiled areas.
In the Australian construction sector, the use of control joints is guided by AS 3958.1-2007 (Guide to the Installation of Ceramic Tiles), which provides specific recommendations for spacing and placement. According to the standard, control joints should be installed:
- At intervals of no more than 4.5m in both directions for internal tiling.
- At changes in substrate type, such as where tiles meet different materials.
- Around the perimeter of tiled areas, including walls and floors.
Control joint calculations are not required for this example and would only be necessary for large, tiled areas, such as common areas or balconies.
Expansion Joints
Expansion joints are essential in construction to accommodate the natural movement of building materials caused by temperature changes, moisture variation, and structural loading. These joints prevent cracking, buckling, and other forms of structural damage by allowing controlled movement in concrete slabs, walls, and other building elements.
In Australia, the design and placement of expansion joints must comply with AS 3600:2018 (Concrete Structures) and AS 3700:2018 (Masonry Structures). For concrete slabs, expansion joints are typically spaced at intervals of 12–15 metres, depending on the environmental conditions and the slab’s design. Similarly, for masonry walls, joints must be carefully positioned to accommodate thermal and moisture expansion, usually at 6–8 metre intervals or near corners and openings.
The use of flexible sealants and compressible fillers, as specified in AS 2870:2011 (Residential Slabs and Footings), ensures the joints remain watertight while allowing movement. Properly designed and installed expansion joints enhance the durability and safety of structures in Australia's diverse climate conditions, from extreme heat to heavy rain.
Expansion joints are not required in this example and would only be necessary for construction joints in concrete if you are tiling over such areas and need a movement joint.
Sealing
Sealing is a critical step in tiling within the Australian construction sector, ensuring durability, water resistance, and long-term performance. Proper sealing prevents moisture ingress, mould growth, and tile delamination, particularly in wet areas such as bathrooms, kitchens, and laundries. According to AS 3740:2021 – Waterproofing of domestic wet areas, all tiling in wet areas must be applied over a compliant waterproofing membrane to meet Australian standards.
Sealers are often applied to porous materials such as natural stone, ceramic and grout, providing additional protection against staining and wear. For external tiling, compliance with AS 4654.1-2012 – Waterproofing membranes for external above-ground use ensures tiles are safeguarded against harsh weather conditions. Following these standards not only enhances the longevity and appearance of tiled surfaces but also guarantees compliance with Australian regulations, ensuring quality workmanship and client satisfaction.
Typically, porcelain or ceramic tiles do not require sealing unless specified by the supplier. However, natural stone tiles should be sealed to prevent colour loss and grime build-up over time.
Acoustic Underlay
Acoustic underlay is a vital component in the Australian construction sector, particularly in multi-residential and commercial projects where noise reduction is a priority. It is designed to minimise impact sound transmission through floors, ensuring compliance with the National Construction Code (NCC) and meeting requirements outlined in AS 3740:2021 (Waterproofing of Domestic Wet Areas) and ISO 140-7 (Field Measurement of Impact Sound Insulation).
When installed beneath tiles, acoustic underlay enhances sound insulation while providing a stable, flexible base to support the tile finish. Common materials include rubber, cork, or high-density foam, with the choice influenced by project-specific requirements such as the building’s acoustic performance ratings and substrate conditions.
In Australia, selecting the right acoustic underlay is essential to achieve compliance with AS/NZS 2107:2016 (Acoustics – Recommended Design Sound Levels), which dictates acceptable indoor noise levels for various spaces. Proper installation also ensures compatibility with the tile adhesive and prevents movement or cracking in the finished flooring.
Acoustic underlays are increasingly specified in strata developments to meet strict soundproofing regulations, demonstrating their importance in maintaining both regulatory compliance and occupant comfort.
Acoustic underlay is not required for this project as it is based on a residential dwelling. However, if this were a high-rise apartment and the bathroom was located above a habitable area on the floor below, then acoustic underlay would be required in that room to reduce footstep noise transferring to the level below.
Pedestal System
In the Australian construction sector, pedestal systems, commonly referred to as "pods," are increasingly used for laying tiles on external areas such as balconies, rooftops, and terraces. These systems consist of adjustable pedestals that create a stable, level surface for tiles, while allowing water drainage underneath, which is essential for preventing moisture buildup and potential damage. According to AS 3958.1:2007 - Ceramic Tiles – Guide to the Installation of Ceramic Tiles, pedestal systems must be installed in compliance with the manufacturer's guidelines, ensuring that the correct height and spacing are adhered to for optimal performance. The benefits of using pedestal systems include enhanced durability, ease of maintenance, and the ability to accommodate uneven surfaces, making them a popular choice for high-performance external tiling projects in Australia.
The pedestal system is only applicable to outdoor areas and is not required for this particular example. However, for reference, ensure that the tile thickness is at least 30mm. The number of pods required per square metre will vary depending on the tile size:
- For 300mm x 300mm tiles, you will need 10 pods per m².
- For 300mm x 600mm tiles, you will need 8 pods per m².
- For 600mm x 600mm tiles, you will need 6 pods per m².
Final Thoughts
The complexity of tiling works requires accurate estimation, a keen understanding of the necessary materials, and a detailed approach to each element, from waterproofing to trims and screeding. Estimating tiling packages for Australian construction projects involves much more than just calculating tile coverage it requires factoring in waste, breakages and other variables that can significantly impact project outcomes. Using tools like digital take-offs, consulting with suppliers and adhering to Australian standards ensures that tiling works are executed seamlessly.
Are you seeking assistance with tiling estimates or looking to gain a clearer understanding of the materials needed for your projects? Contact us today! We specialise in tiling, waterproofing, and screed services for residential, commercial, and industrial spaces. Our team is dedicated to providing a professional and tailored approach to meet your specific needs. Let us help you achieve the best results for your next project.
Other insights
Accurate Estimating Services for Builders
Accurate estimating services are the key to keeping your construction project on track. Discover how professional estimating can save time, reduce cost and boost profit margins.
Tiling Take-Offs for Commercial Tiling Companies: Unlocking Competitive Bids in Tier-1 Projects
Ensure your commercial tiling bids are precise and competitive with expert tiling take-offs from Pekaj Group. Save time, reduce costs and win more Tier-1 projects with our comprehensive services.
Contact us now to leverage our expertise in cost estimation and planning.
Let's build success together.
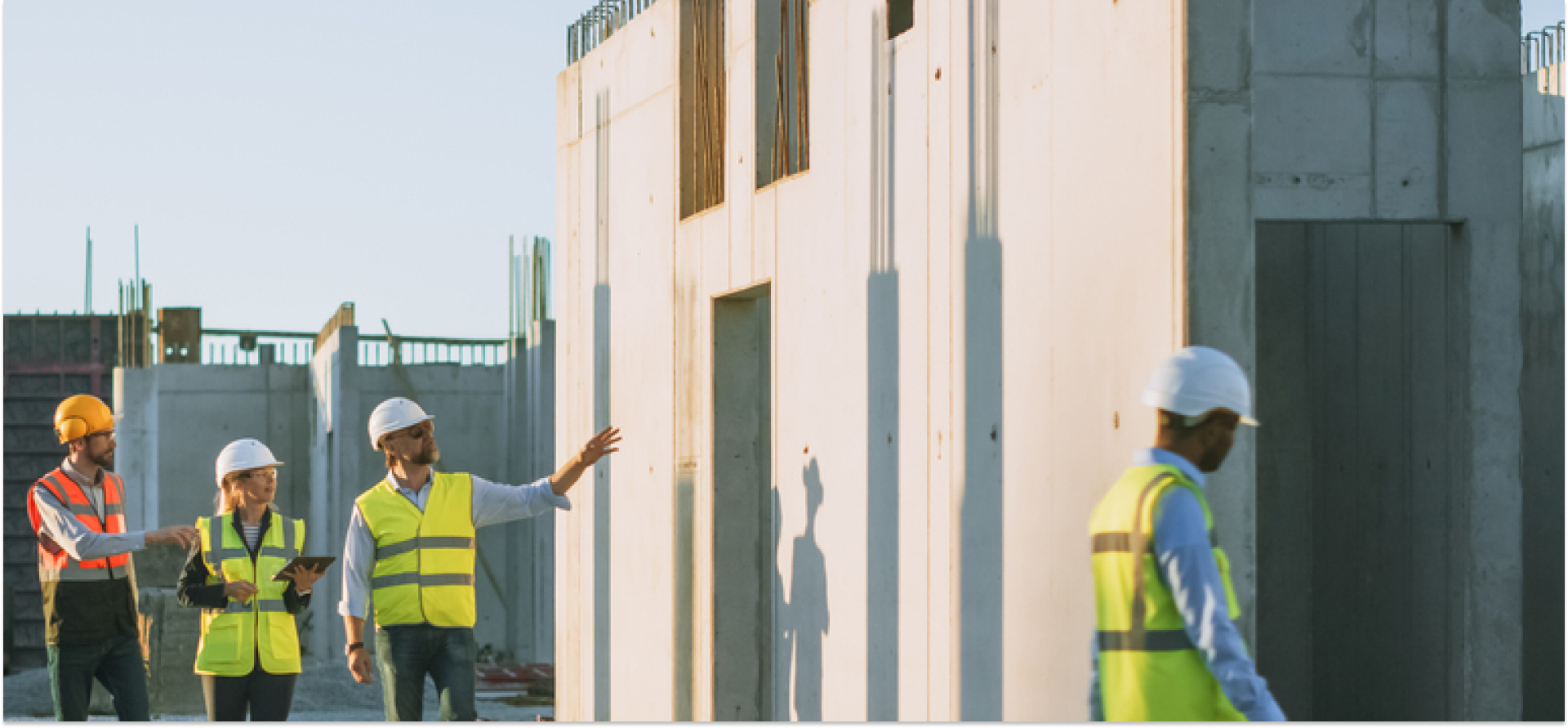