Waffle Pod Construction in Australia
A Comprehensive Guide to Calculations and Requirements
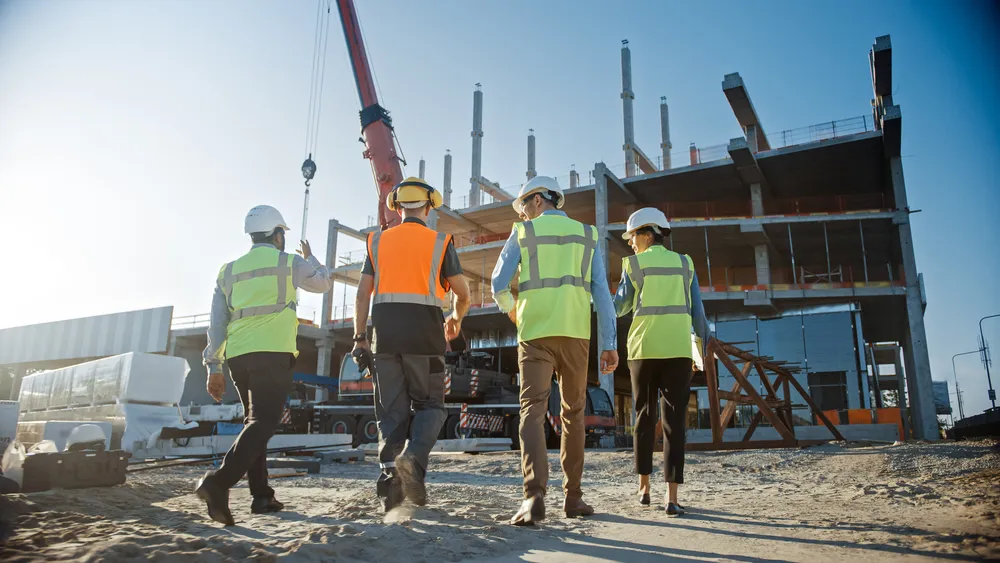
Waffle Pod Construction in Australia
In the ever-evolving field of construction, engineers and builders are constantly seeking innovative methods to enhance efficiency, reduce costs, and improve environmental sustainability. One such method which has been gaining popularity in Australia for the past 20 years is the use of waffle pod slabs, a modern foundation system that combines strength and versatility. In this blog post, we will delve into the intricacies of waffle pod slabs and walk through the calculations involved in their construction.
Understanding Waffle Pod Slabs
Waffle pod slabs consist of a grid of voids (pods) separated by reinforced concrete beams. These pods serve multiple purposes, including reducing the overall concrete volume, providing insulation, and facilitating better control of ground movement. The use of waffle pods is particularly beneficial in areas with challenging soil conditions.
The waffle pod represents an advanced approach to concrete slab construction, involving on-ground construction rather than in-ground. This eliminates the necessity for trenching leading to cost savings and enhancing construction durability and strength. Waffle pods, despite their lightweight nature, are robust enough to support the weight of numerous construction workers and wet concrete during site preparation and pouring. Installation takes place on cleared, level surfaces, ensuring that inclement weather is not a hindrance. Additionally, each waffle pod slab provides exceptional strength and durability while simultaneously reducing construction costs.
Which Slab is Superior: Waffle Pod Slab or Raft Slab?
This is a very common question that is asked and ultimately it will be dependent on the engineer and budget of the client. Both construction methods have their merits based on specific circumstances. While waffle pod slabs are cost-effective and easier and cheaper to construct, some builders prefer raft slabs under certain site conditions.
Raft slabs are most suitable for:
1. Very soft ground, particularly if it's prone to movement
2. Sloping building sites
3. Areas with high winds or cyclones
Soil classification and suitability of waffle slab?
The table presented below offers a concise summary of the appropriateness of the waffle slab system in different soil conditions.
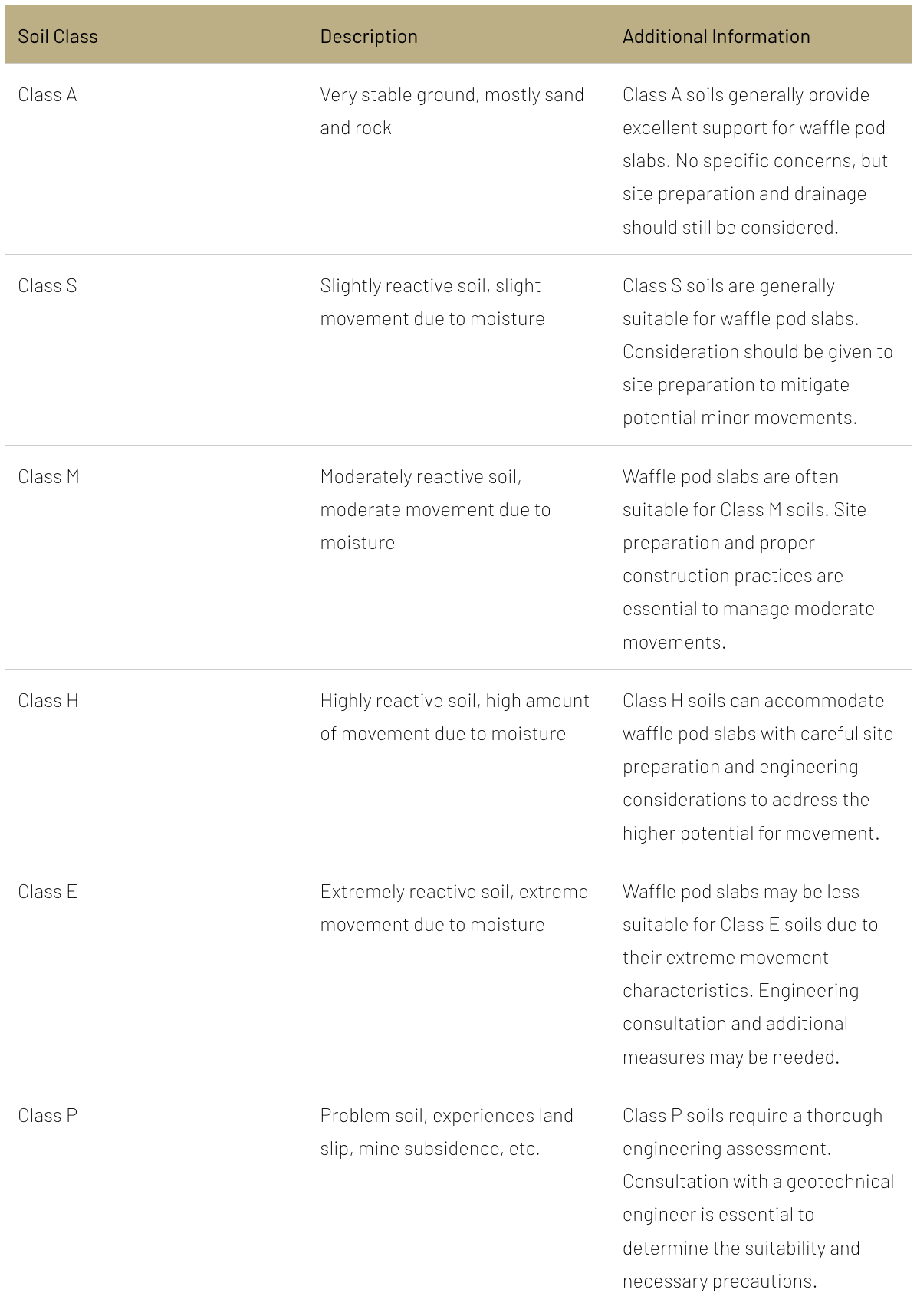
Calculating Materials for Waffle Pod Slab Systems:
Estimators and quantity surveyors must carefully calculate the materials needed for a waffle pod slab system. In this blog post, we will perform a thorough calculation of all elements from first principles, offering a comprehensive guide on the materials, labour, and costs involved.
Bluebeam Revu is the chosen software for performing the planned measure. Renowned for its speed and efficiency in measuring take-offs, this software is extensively utilised by residential and commercial builders. It stands out as one of the key tools employed by Pekaj Group Pty Ltd for estimating purposes.
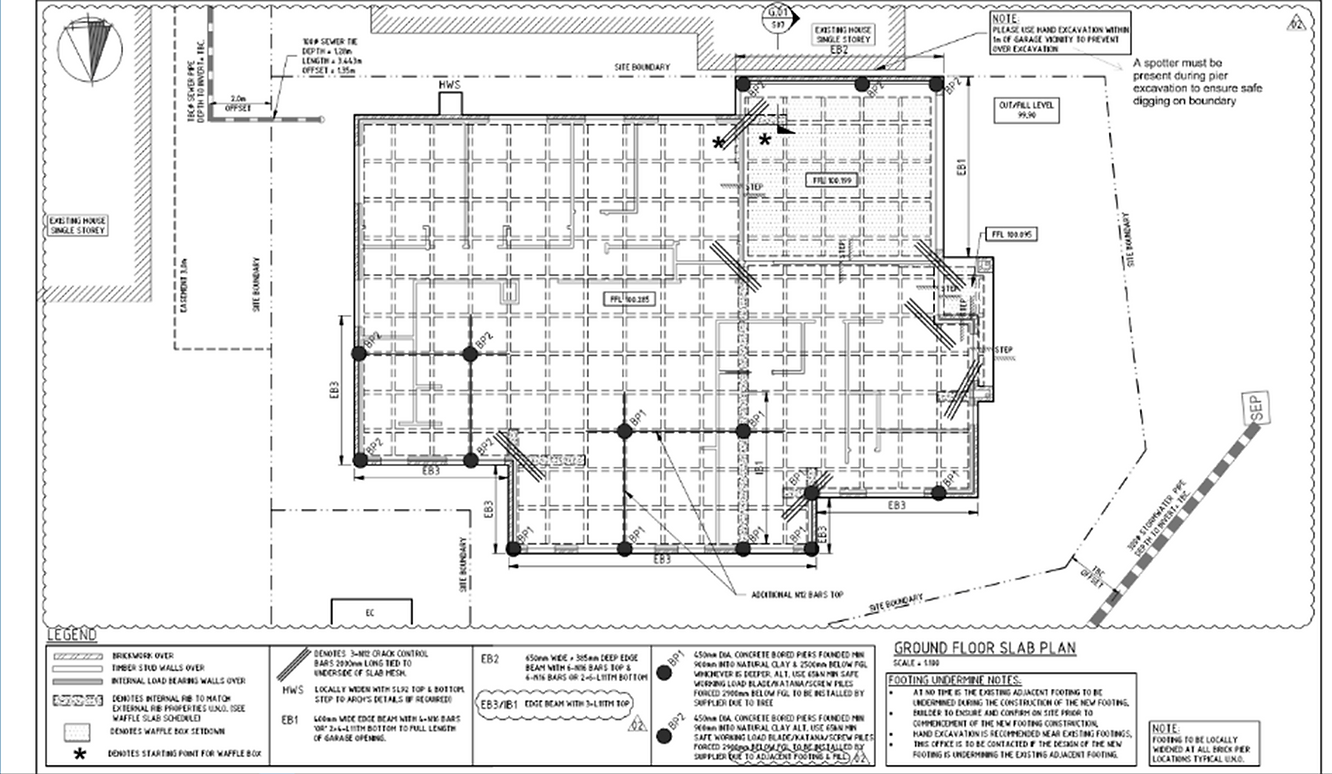
Based on the attached engineered ground floor slab plan the following elements will need to be determined which will be used for a variety of calculations.
- Edge Beam (External Rib)
- Internal Beam (Internal Rib)
- Slab Area
- Bored Piers
Edge beam is determined by measuring the external perimeter wall. In this example we have 3 different sizes for the edge beam.
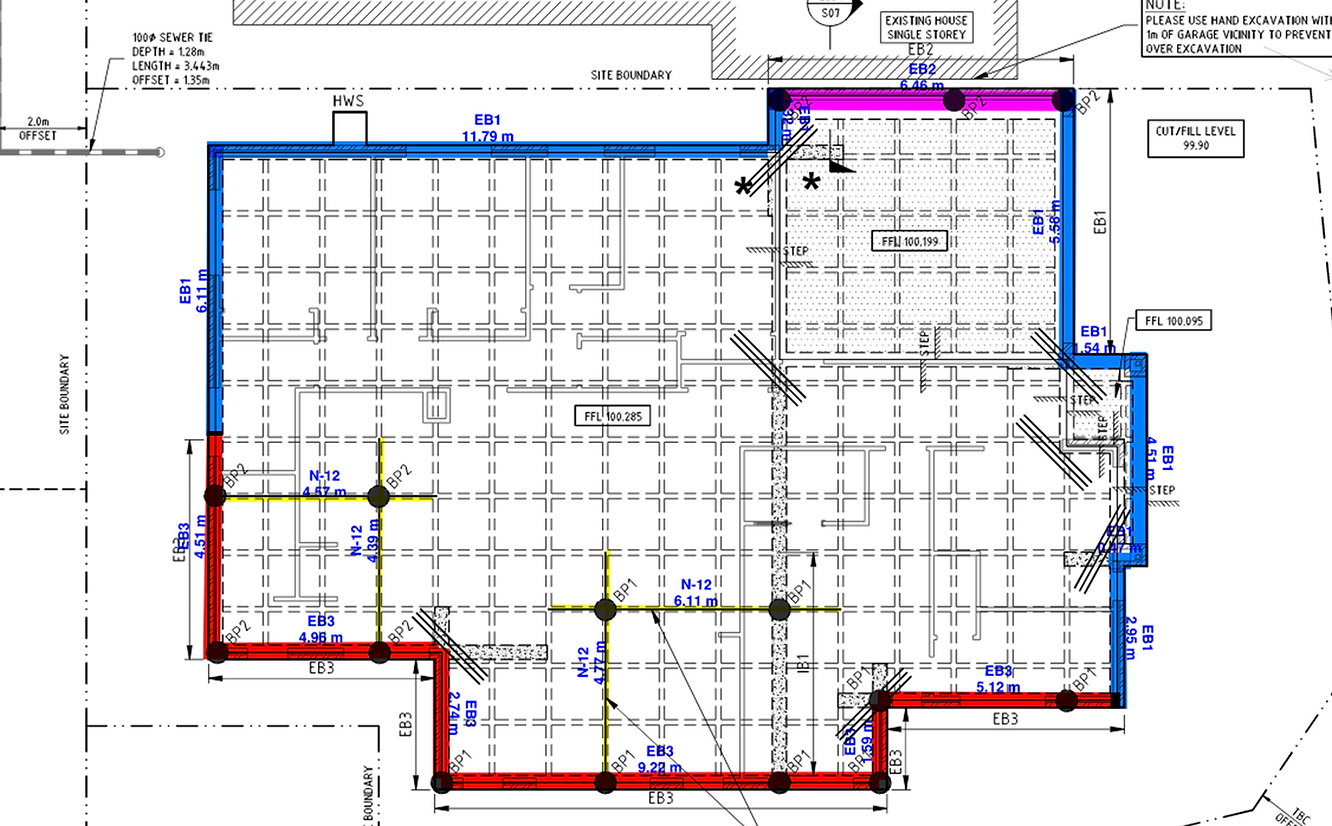
The different sizes represent different width and depth requirements hence needing to be measured individually.
- EB1 - 34.26m (Blue)
- EB2 - 6.46m (Pink)
- EB3 - 28.14m (Red)
The same principle is used to determine the internal beams. In this example we have two elements to measure.
- IB1 - 337.49m (Pink)
- IB2 - 26.13m (Red)
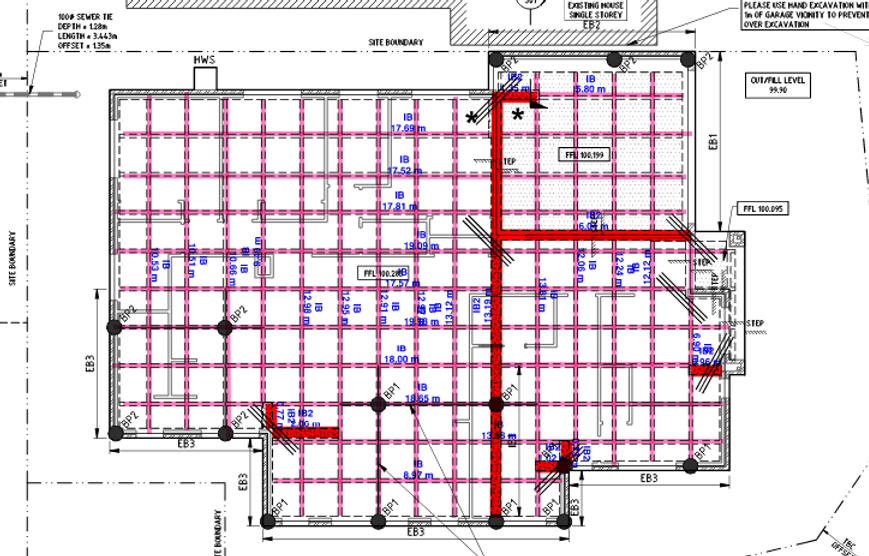
The next element to measure will be the actual slab area. Highlighted in green the total area equates to 246.35m2.
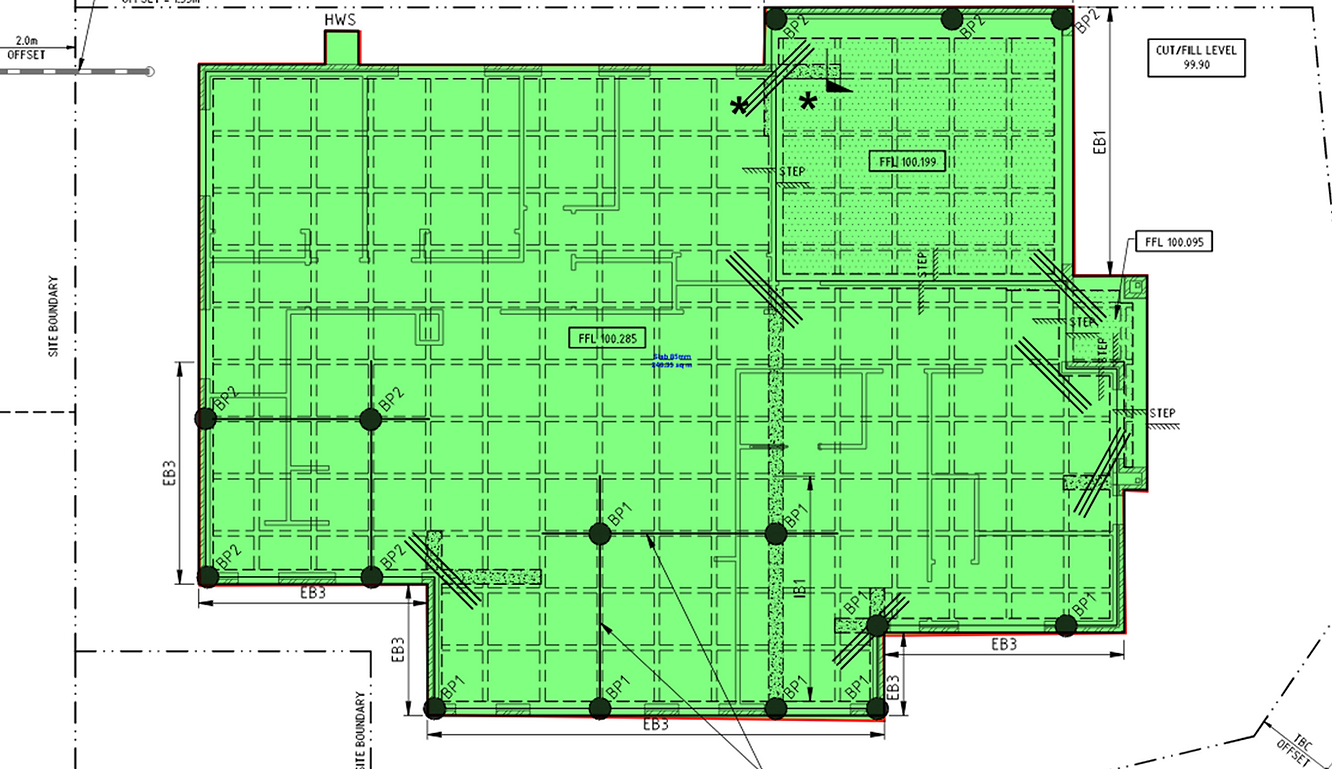
The last element to measure is the bored piers. There are two types consider for this project.
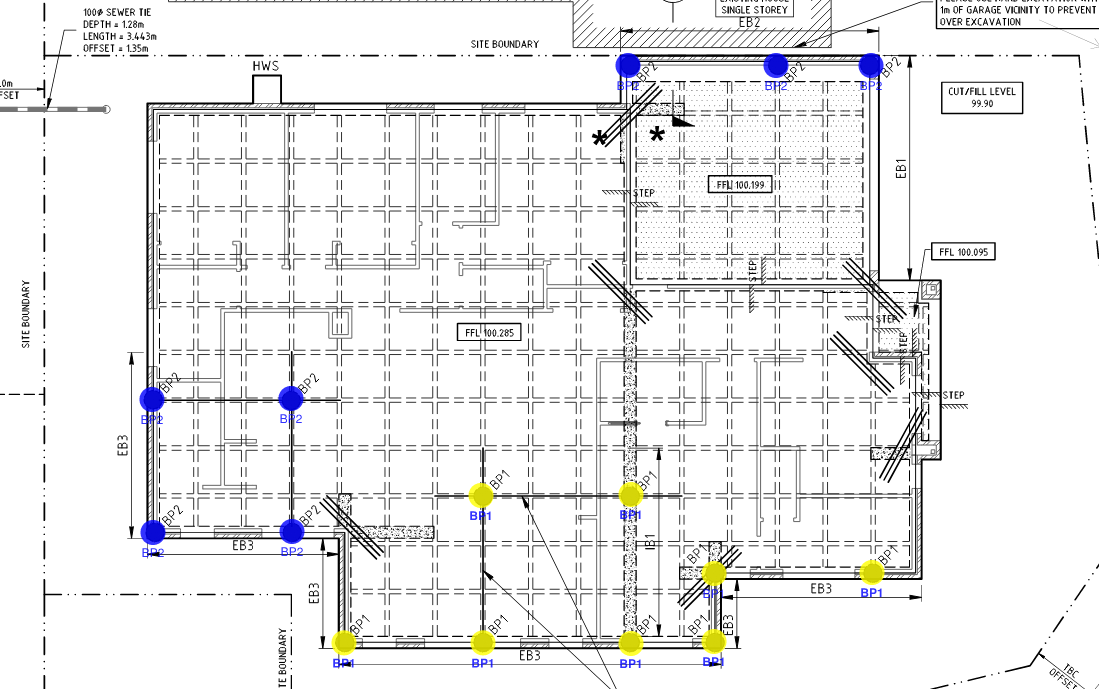
- BP1 - 8 No. (Yellow)
- BP2 - 7 No. (Blue)
Now that the initial measure has been completed, we can finally workout the associated elements to determine the total volume of concrete, reinforcement, waffle pod accessories and labour for the project.
Concrete
In order to determine the total volume of concrete for the project the following calculations need to be determined. But before that you will need to review the engineering drawings to make sure you have identified all the elements to use in your calculation from the waffle slab schedule.
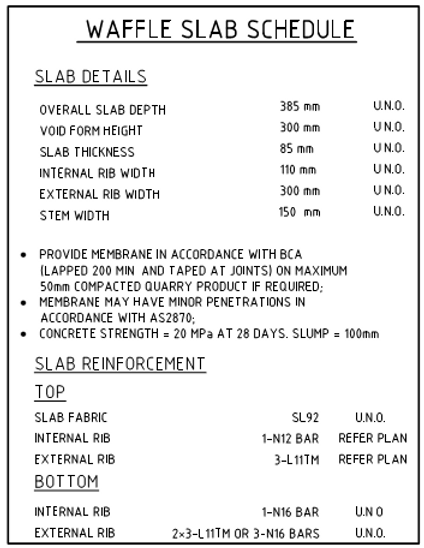
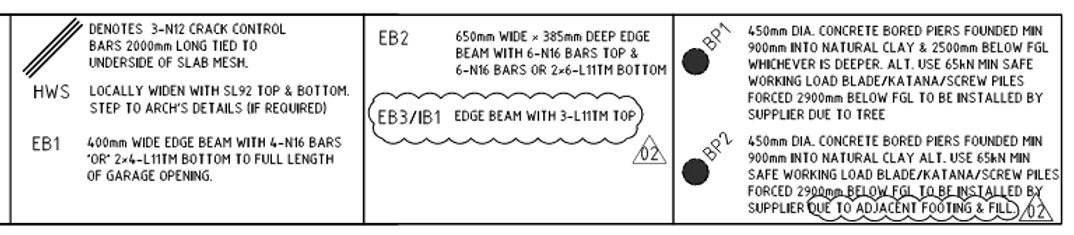
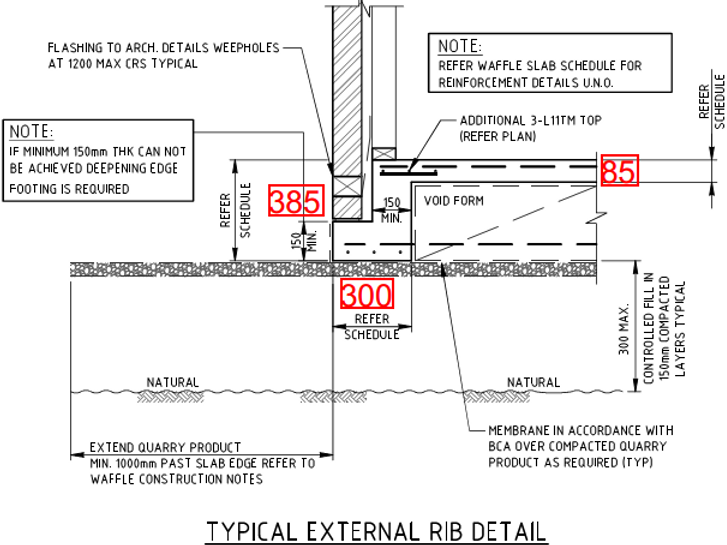
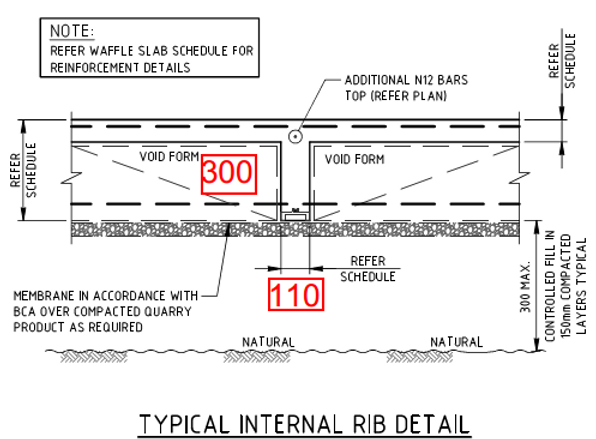
Now that the individual elements have been identified the below table will assist with the formula and calculation for this section.
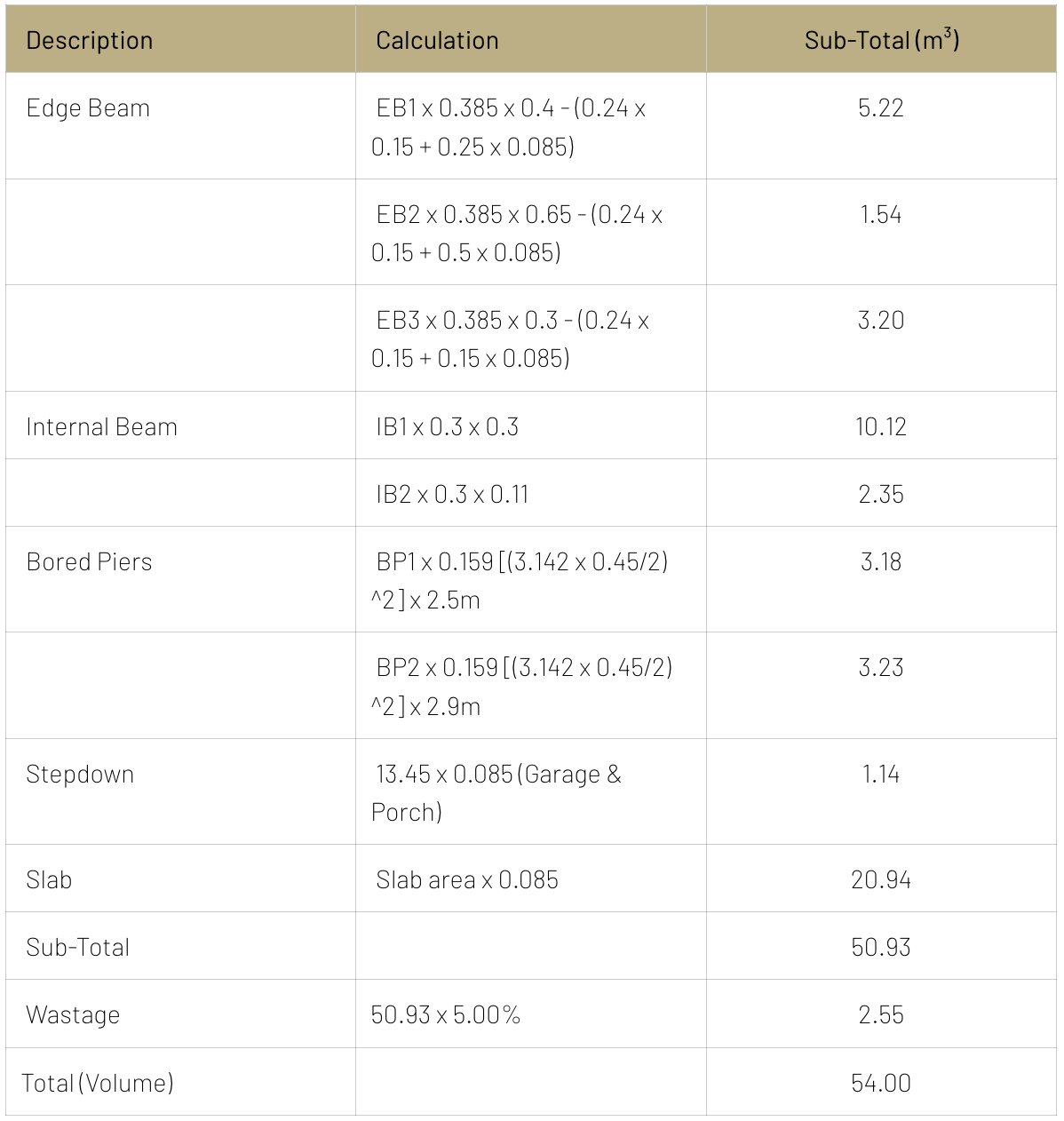
In this example, the overall concrete volume is 54.00m3. Theoretically, we have accounted for concrete across all designated areas. However, in practice, there's a possibility of falling short, despite our thorough preparation.
Several factors can contribute to a shortfall in concrete:
- Inaccurate cutting of pods to fit in the designated space.
- The concreter opting for a 100mm slab thickness instead of the specified 85mm.
- Wastage and spillage during the concrete application.
- Deviation from the intended concrete mix.
- Bored piers cut wider and deeper than originally anticipated due rock floaters.
This method from first principle of calculating is hardly used, and most companies now use industry-based averages for waffle pod systems. The following averages are considered reasonable and have stood the test of time.
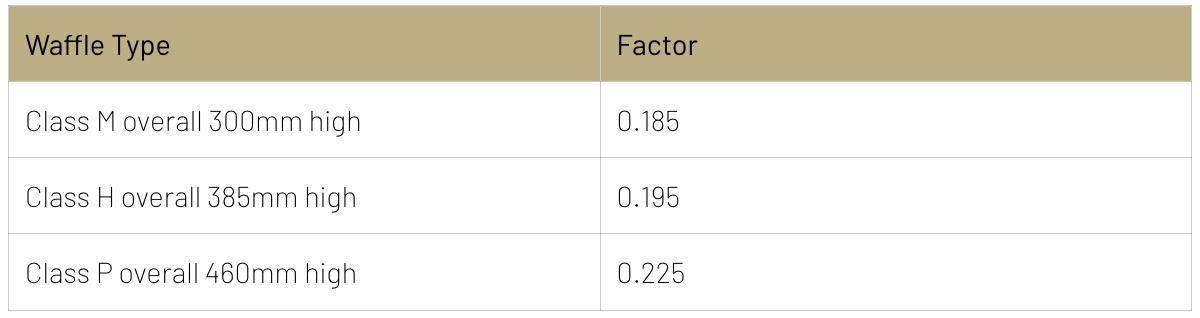
The amount of concrete required for this project using industry-based factors would be as follows:
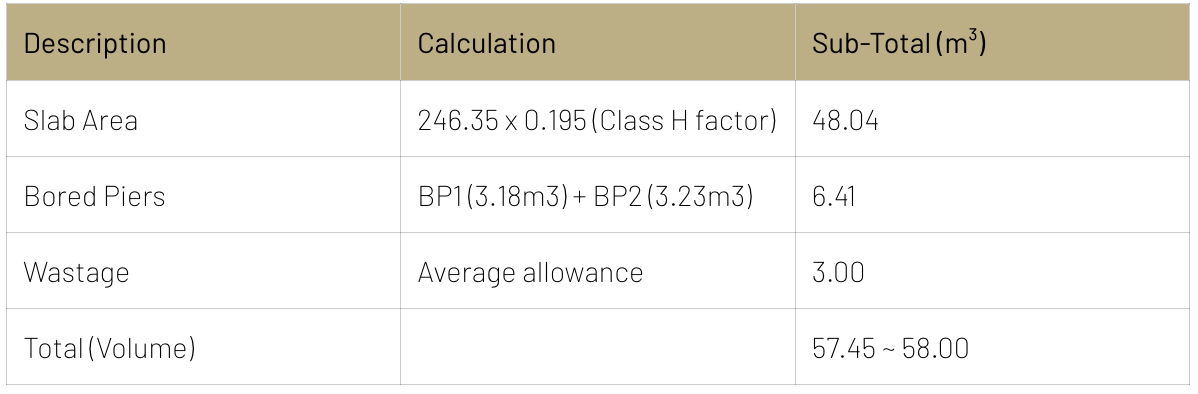
Based on industry-related considerations, there is a 4.00m3 disparity in the overall concrete volume. Both methods of calculating the concrete volume are accurate. Now, the decision of which answer to adopt becomes a bit more intricate. One viable approach involves generating two purchase orders for the project. Purchase order 1 would cover 54.00m3, while purchase order 2 (4.00m3) would serve as a contingency, only to be utilised if the on-site concrete quantity exceeds the initial estimate.
Reinforcement
Reinforcement is required in waffle pod construction to enhance the structural integrity and load-bearing capacity of the concrete slab. While waffle pod slabs utilise void-forming pods to reduce the overall weight of the concrete and minimise resource usage, the reinforcement serves to address specific engineering requirements.
Key reasons for reinforcement in waffle pod construction include:
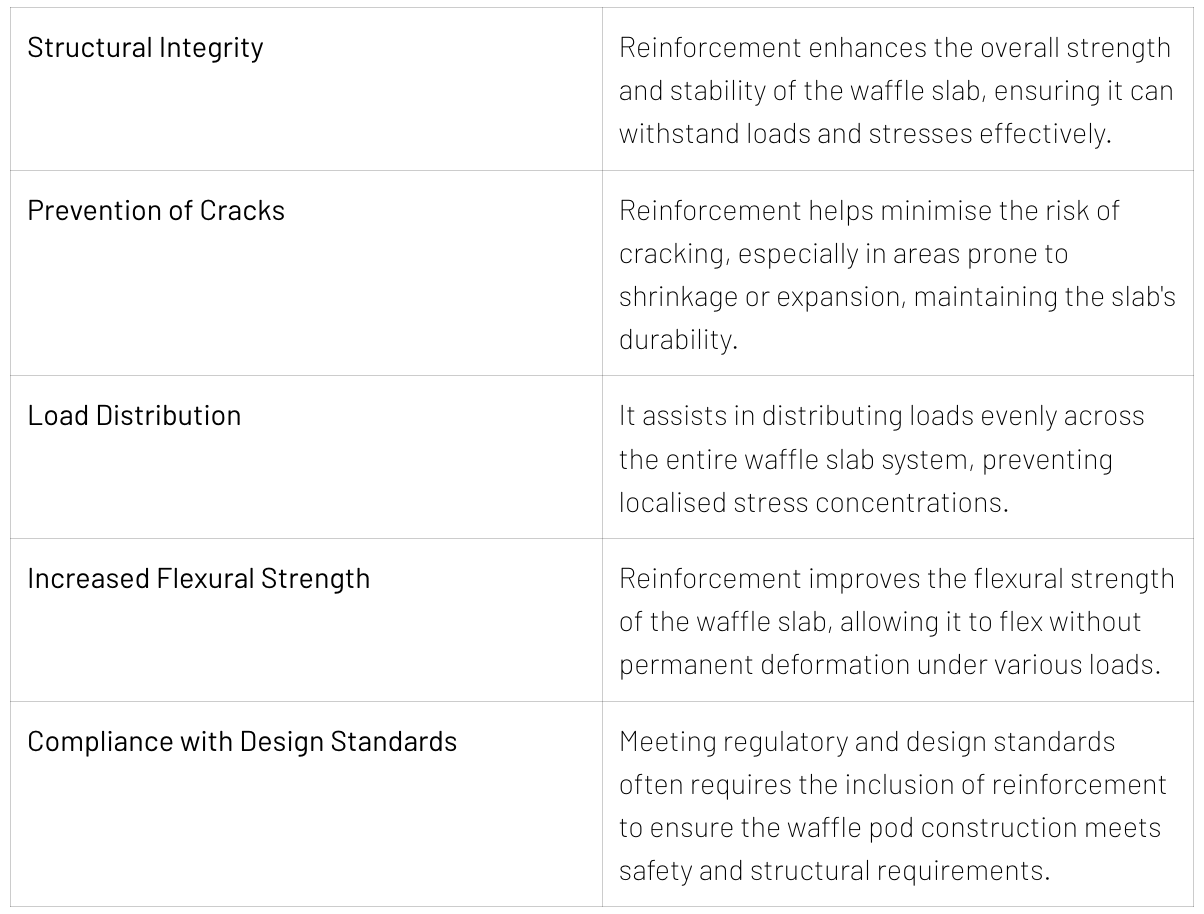
Taking into account the above noted we will now review the engineering plans to identify the various types of reinforcement required for this project.

Waffle Pod Accessories
The table below provides a quick overview of the main accessories to consider when ordering. You will need to find out from various suppliers if there are pack sizes so you can round up your quantities accordingly. You will also need to consider deliveries if you are purchasing from several suppliers in your costings.
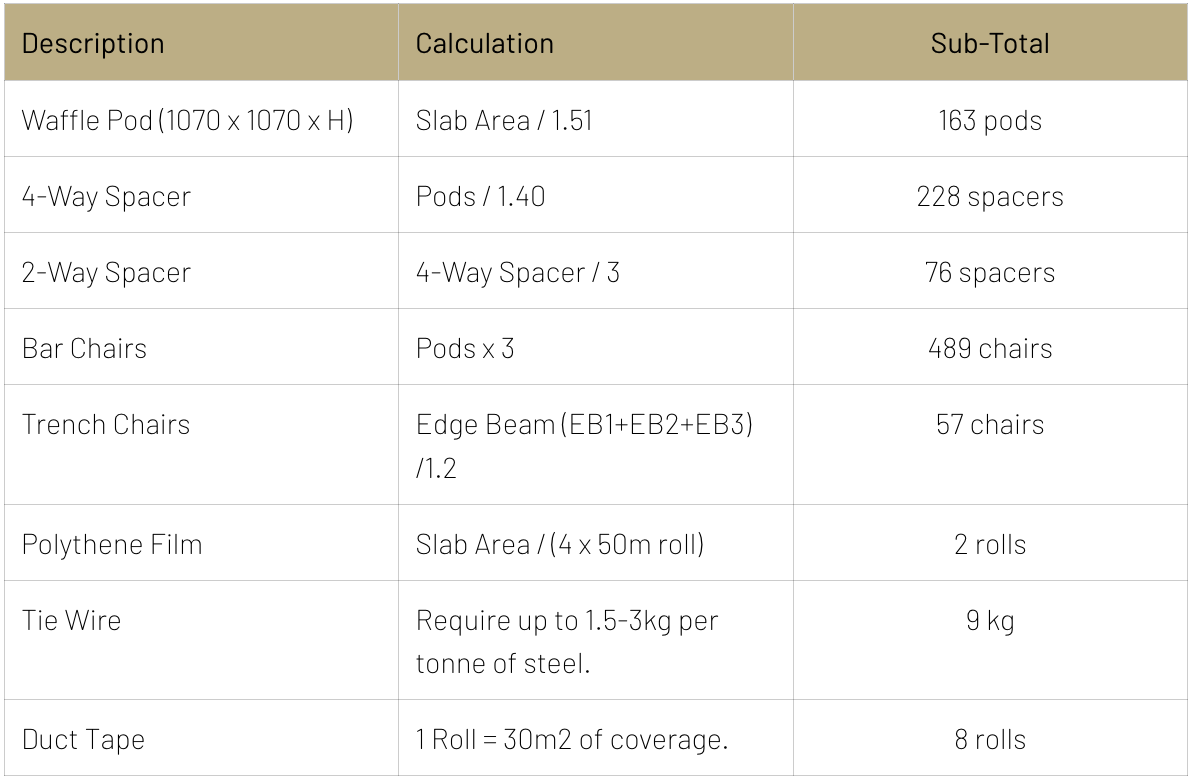
Labour
Determining this component is challenging due to the numerous unknown factors involved. Initially, it involves a trial-and-error approach, as different contractors have unique methods and pricing strategies for projects.
For this project, we have compiled a list of tasks to take into account when determining the pricing for this specific portion of works.
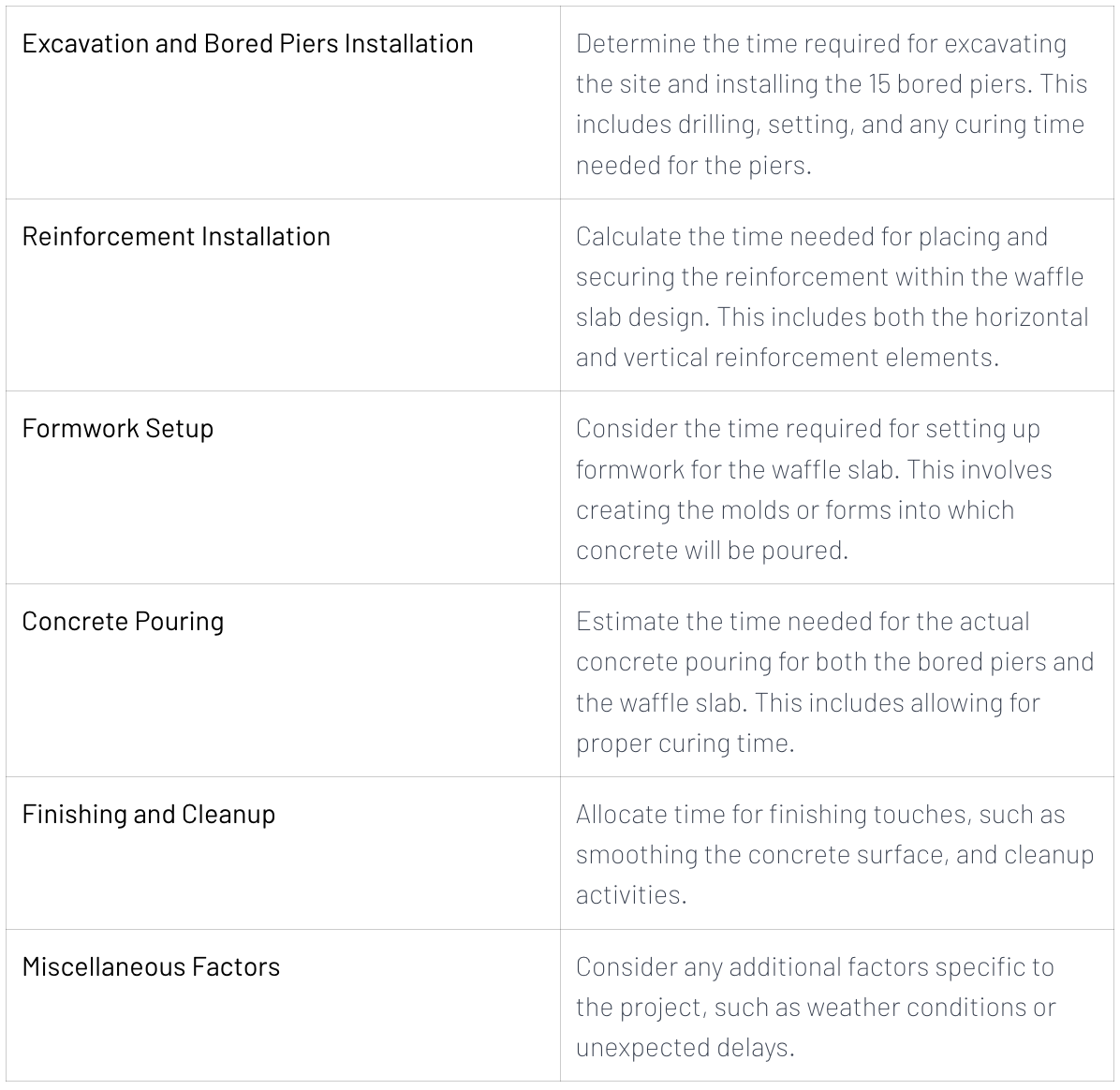
Taking into consideration the above noted we will determine the number of days to complete task and size of team (gang) required.
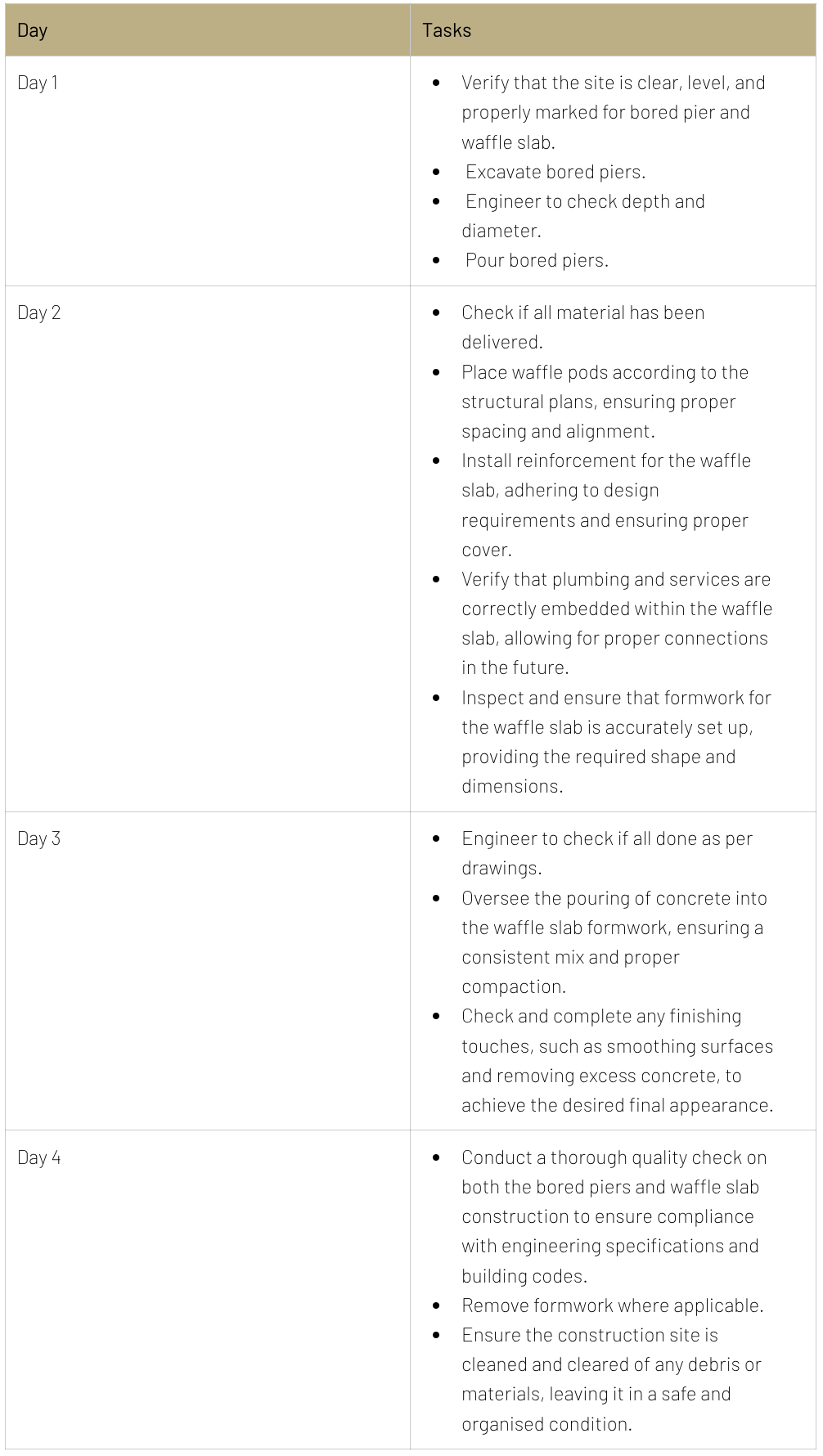
Having determined the duration for task completion, it's crucial to factor in the labour component. Using the industry average rate for concrete labouring in Melbourne at $50.00 per hour and considering a gang size of 4, the daily labour cost is estimated at $2,000. For a 4-day duration, the labor costs should amount to approximately $8,000. It's worth noting that gang sizes for concreting typically range between 3 and 5 for residential construction projects.
Summary of Costs
The table below offers a summary of the cost considerations for this project. The price ranges presented are averages specific to the Melbourne region. It is important to note that these figures serve as general estimates, and for a more precise cost assessment, it is recommended to obtain pricing information from your local supplier.
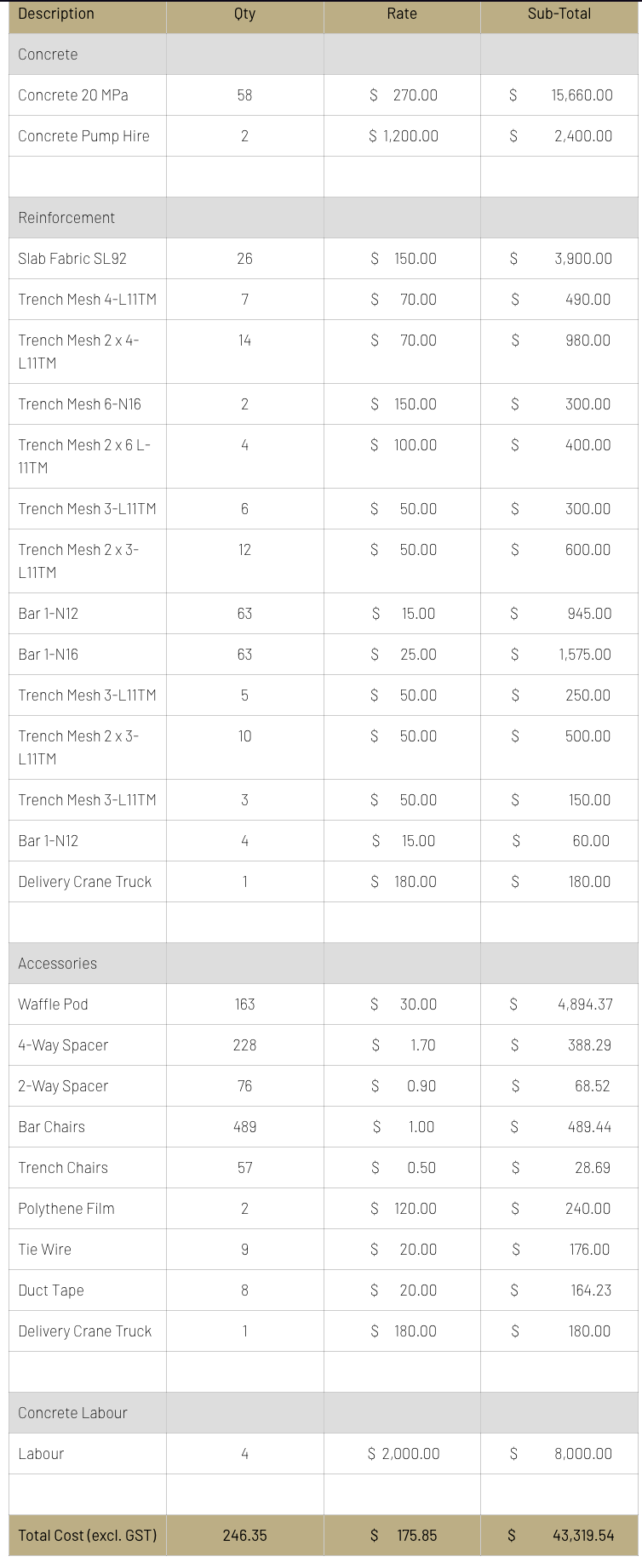
For this specific project, the comprehensive cost for concrete (including supply and installation) is approximately $43,319 plus GST. Breaking this down per square meter, it equates to around $176.00/m2 or $1,633 per square.
As quantity surveyor or estimator, the calculated cost serves as the initial budget for the project. Upon obtaining quotes from your sub-contractors, you can assess whether this budgetary allowance is adequate. This evaluation helps determine if any adjustments are necessary for the current project or if modifications are needed for future projects.
At Pekaj Group Pty Ltd., who provide quantity surveying and estimating services in Melbourne and across Victoria have developed specialised templates (preliminary estimates, detailed estimates, material take-offs and bill of quantities) that ensure that your projects cost estimates have the information you need to make informed decisions about your project.
Conclusion
Thank you for investing your time in reviewing this in-depth analysis of a waffle slab take-off. It's important to acknowledge that the outlined approach may not be universally applicable, and it is recommended to evaluate each project individually.
The insights derived from elements based on first principle offer valuable perspectives and contribute to a more nuanced understanding of the subject matter. Taking these factors into account will undoubtedly improve your skills as an estimator, contributing to more effective project evaluations and decision-making processes in the future.
Other insights
Accurate Estimating Services for Builders
Accurate estimating services are the key to keeping your construction project on track. Discover how professional estimating can save time, reduce cost and boost profit margins.
How to Professionally Perform a Tile Take-Off: A Comprehensive Guide for Builders and Tiling Companies
Master the art of tile estimating! Discover essential techniques, avoid costly mistakes and ensure seamless finishes for any project with our comprehensive tiling guide.
Contact us now to leverage our expertise in cost estimation and planning.
Let's build success together.
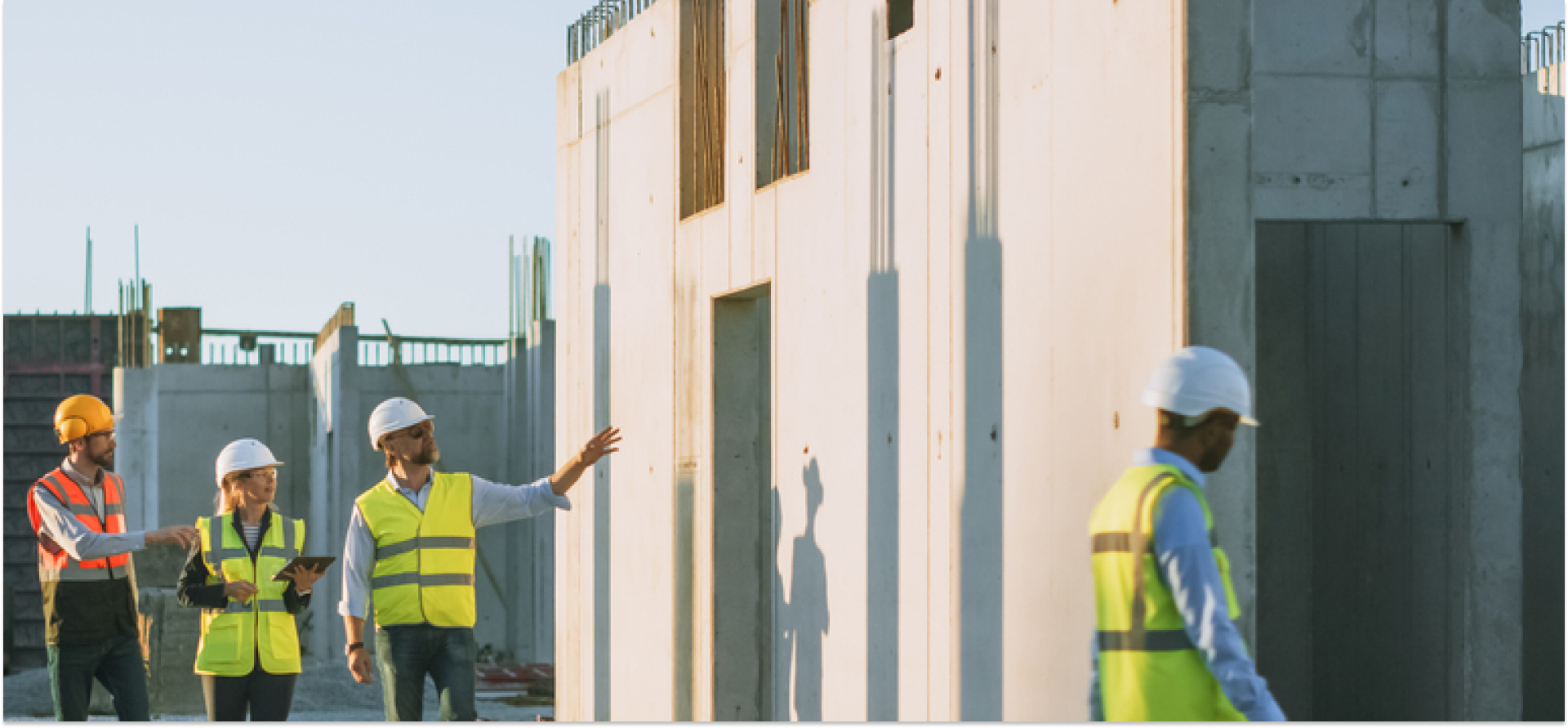